Main Features:
- Front supports : 2 pieces, ensuring stability during bending operations
- AUTOMATIC X axis on servo motor!!!
- Axes Y1, Y2 , – AUTOMATIC on servo motor!!!
- R axis – AUTOMATIC on servo motor!!!
- Automatic adjustment of the deflection arrow
- Automatic deflection compensation
- Front bracket on linear guides
- SERVO 11kW motor reduces current requirements , ensuring more stable operation
- Independent stainless steel oil tank
- Laser line for easy positioning of bent objects
- As standard, the machine is equipped with hardened, split punches and 4V dies (42CrMo)
Machine Description
Ultimate press brakes are an advanced tool used in the industry for edging and bending materials. They are a versatile machine that allows precise and efficient finishing of edges on a variety of materials, such as steel, aluminum and plastics.
Ultimate press brakes are designed with efficiency and reliability in mind. They feature a solid construction that ensures stability during operation. The machines also feature advanced control systems that allow programming of various operating parameters, such as edging speed, bending angle and press force.
One of the main advantages of the Ultimate press brakes is their ease of use. The intuitive user interface allows the operator to easily program and control the machining process. Additionally, the presses are equipped with advanced safety systems that ensure safe use. Thanks to their high performance, the EASY press brakes are the ideal solution for manufacturers who require fast and precise edge processing. It can be used in various industries, such as the metal industry, carpentry, furniture production and the plastics industry.
Why a CORMAK press brake?
- When designing it, emphasis was placed on versatility of use, which is why it is suitable not only for bending sheet metal but also for crimping and notching it, and during each of these operations it does not lose what is most important: reliability and precision .
- European-made press , manufactured in accordance with all machinery directives.
- With a declaration of conformity - CE.
- The production uses components from renowned global manufacturers such as: Bosch Rexroth pumps , Schneider Electric electrics , servo motor control, Cybelec or Delem control.
- Heavy and stable frame construction for precise work
Laser protection system as standard
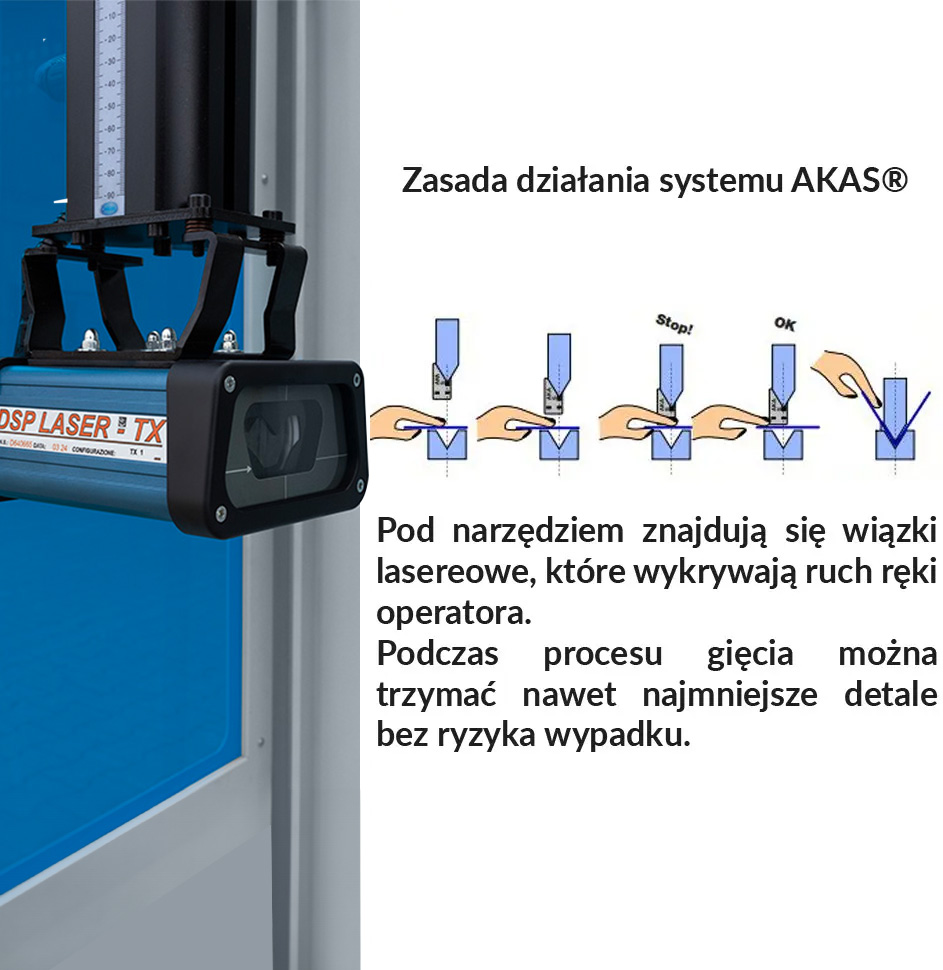
- Laser protection of operator's hands: DSP
- The system only works during the boom's rapid run-out.
- Allows the lowest switching points above the material from approach to working speed.
- It does not require any special pedal pressing sequences.
- Allows for quick tool change (automatic positioning of the transmitter with the receiver after changing the tools to a different length type)
- No need to stop in box mode
- Does not increase cycle time in box bending mode compared to other safeguards
- It enables bending of material with an uneven surface (e.g. wavy, uneven, dirty sheet metal) by changing the speed to slow at any point of the rapid movement.
EASY TO USE (INTUITIVE) CYBTOUCH 12PS CONTROL
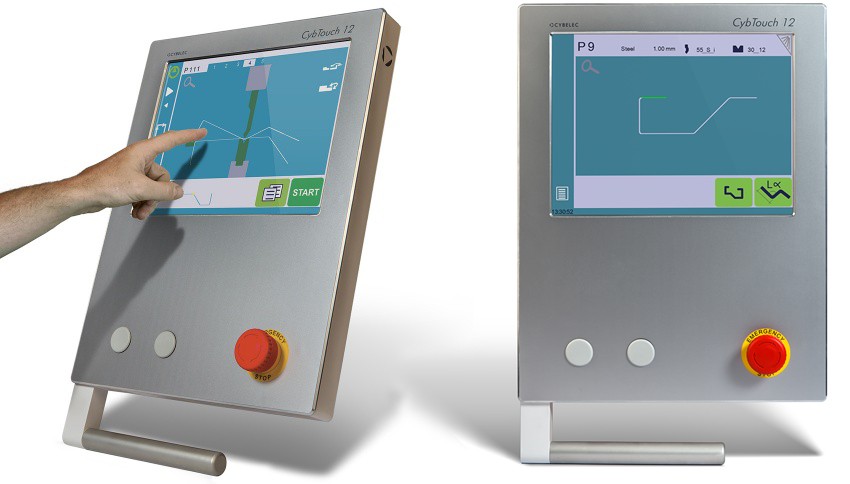
- Large, vibrant, high-contrast touchscreen
- TouchProfile function for hand drawing
- Simple tabs, clear display
- Intuitive and user-friendly interface
- Complete programming for efficient series production with multiple bends
- Easy single bending with the EasyBend tab
- Online Help and Warning Popup
- Convenient software updates and data backups via your PC or notebook
- USB port for memory cards
- Large selection of languages available
- 4-axis control (Y1-Y2-XR)
- Creating 2D TouchProfile graphics with manual sequencing
- Calculating bending allowance
- Calculation of the clamping force for table compensation
- Modular tools for each part or bend
- Calculating the punch depth
- Angle and back gauge correction
- Supplied with PC-ModEva offline software
Technical parameters
Max. thickness of bent sheet metal (S235) |
up to 6.0mm |
Nominal pressure |
1250kN |
Maximum length of bent sheet metal |
3100mm |
Depth of cut in beams (throat) |
320mm |
Maximum stroke of the moving beam |
120mm |
Maximum opening height |
390mm |
Distance between beams |
2700mm |
Rear bumper departure |
600mm |
SERVO engine power |
11.0kW |
Length |
3870mm |
Width |
1550mm |
Height |
2400mm |
Weight |
7500 kg |
Automatic deflection compensation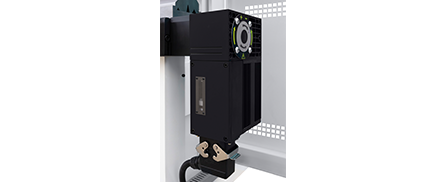
Ensures the same bending angle is maintained along the entire bending length
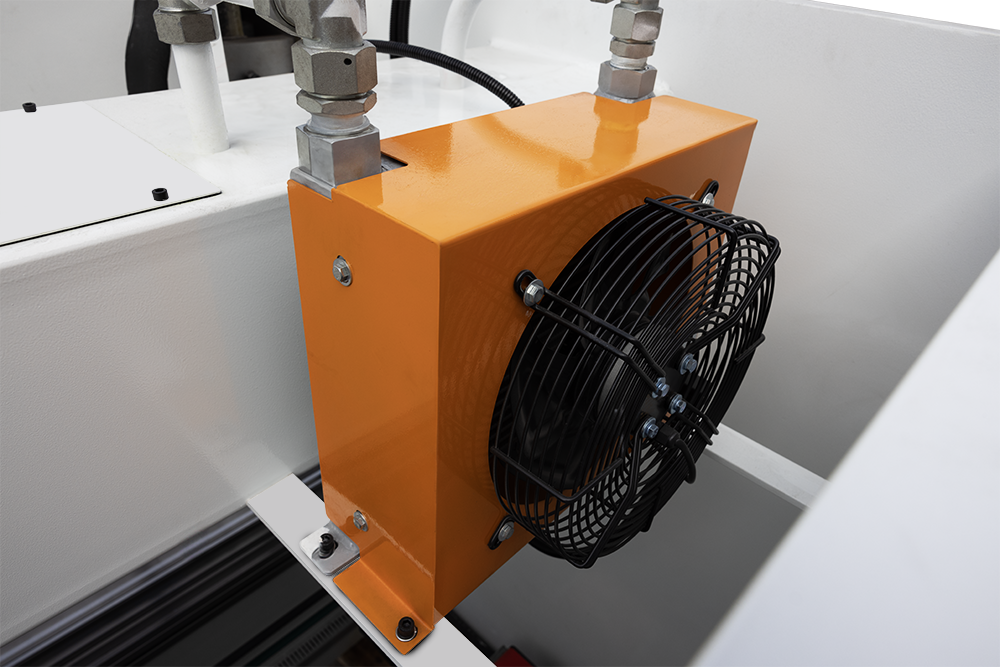
OCS – Oil Cooling System
The SOil Cooling System guarantees the stability of the machine's operating parameters even after long, continuous use.
High quality components:
- Schneider/Delta/Eaton brand electrical system components

- Automatic compensation of the deflection arrow in the work table
- The European mounting system allows for the attachment of standard and specialist tools.
- Brushes on guides
- "Amada" type quick tool clamping system
- Brackets on linear guides
- The integrated hydraulic system (Bosch Rexroth Germany) enables quick switching of the direction and speed of work.

Axes Y1, Y2 - these are the axes responsible for the work of the bending beam. Y1 is the left side and Y2 is the right side. The entire bending process is controlled by the CNC system using a hydraulic system integrated with the measuring system, which consists of measuring rulers located on the left and right side of the machine. CNC-controlled press brakes are synchronous machines, i.e. those that have independent control of the left and right actuator, which allows us to freely correct parallelism and correct the bending angle independently on both sides Y1 and Y2.
X - is the axis responsible for the movement of the bumper in the front-back plane. It is responsible for maintaining the dimension of the bent sides of the detail. It is driven by a stepper motor or servo drive, while the executive mechanism transmitting the drive is ball screws. The encoder is responsible for determining the position and accuracy of the bumper. CNC controls can automatically calculate the X position in order to obtain the appropriate bending dimension, taking into account the thickness, type of material, tools used, bending angle and whether the dimension in the drawing is external or internal.
R - is also the machine's bumper axis, responsible for movement in the up-down plane. It is most often driven by a servo-controlled gear. The encoder is also responsible for position and accuracy. The zero point for the R axis is the height of the currently mounted matrix on the press table. In modern CNC controls, the bumper fingers have several reference planes or sheet metal support, after selecting the bumper position in the control, the machine will automatically correct the R height and the X position of the bumper.
Standard equipment:
- Cybelec CYBTOUCH 12PS (12'') Controller 2D TouchProfile graphics creation with manual sequencing
Fiesler AKAS front safety laser system (Manual)
- Controlled axes Y1-Y2-XR
- Backgauge distance adjustment (X axis) - (engine with encoder) from CNC system
- Beam adjustment (axes Y1-Y2) - (2 hydraulic cylinders controlled by Rexroth valves) from the CNC system
- Amada Promecam type quick tool clamping system
- Measuring rulers - OPKON
- Safety switch on the foot switch
- Two front supports
- Electrics - Siemens, MW, FISSLER, Mitsubishi Electric, ELK, OMEGA
- Hydraulics (solenoid valves) -Rexroth
Optional equipment:
- Cybelec CYBTOUCH 15PS (15'') Controller
- R-axis
- Servo rear bumper Z1, Z2
- Oil heater
- Preparing for the tandem
- Control panel in opposite position
The body of the press brake is made of side walls and a table. The pressure on the table is exerted by the bending beam moving in the body guides. Both the table and the beam are supported at two points. When very large forces are applied to the bent sheet metal, the table deflects. This causes a problem with obtaining the set angle in the middle of the table. In order to obtain the same angle along the entire length of the bent sheet metal, it is necessary to equip the machine with a table compensation system. However, the most commonly used system is a mechanical system. This is the so-called opposite wave system. The press table is milled from the bottom so that two strips with opposite waves fit in it. The lower strip is fixed, while the upper one is moved manually using a crank with a built-in scale or automatically by a servo-driven gear. This system perfectly compensates for the table deformations that arise in the process of bending the sheet metal, while ensuring high accuracy in maintaining the value of the set angle.
Step bending examples:
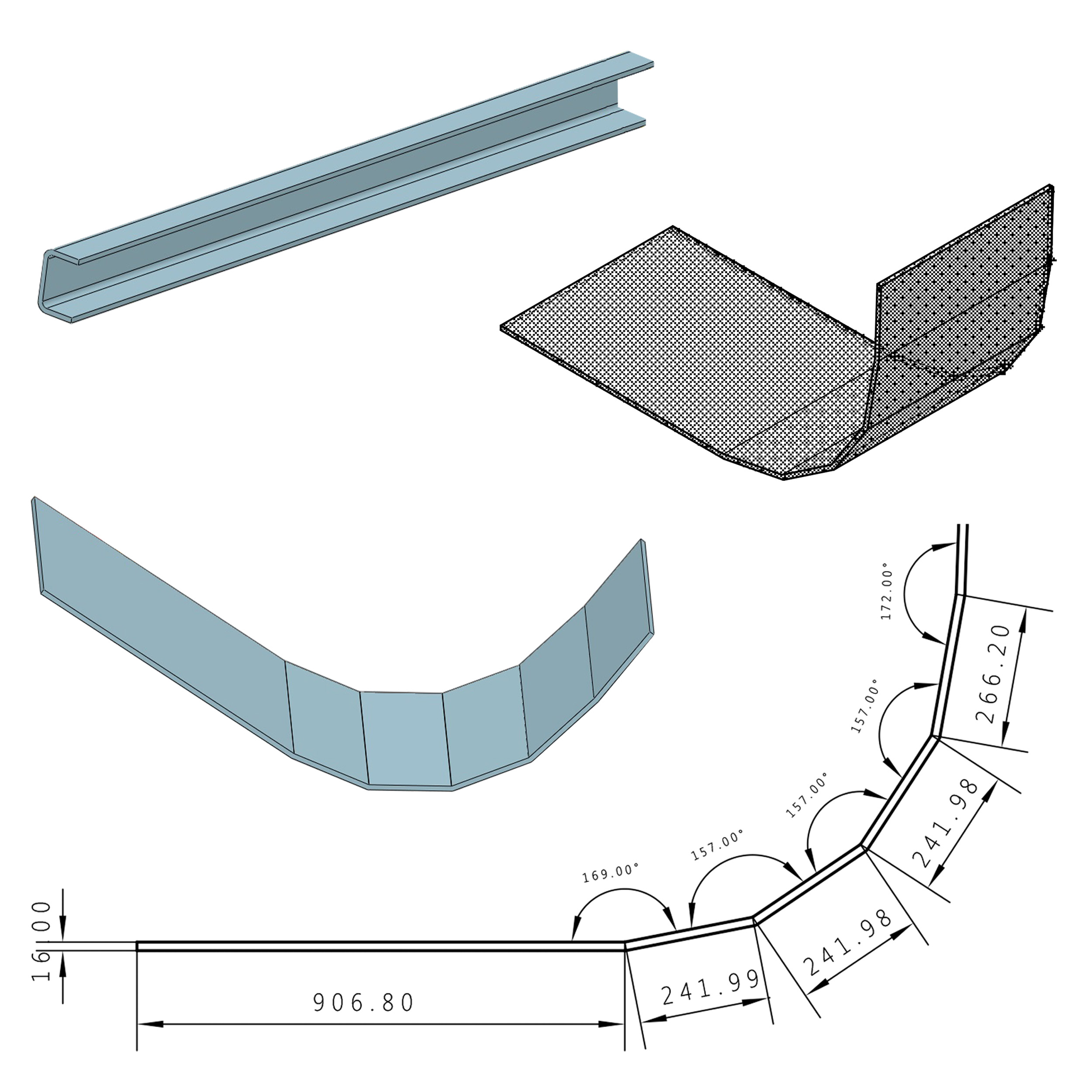
Pressing force selection table:
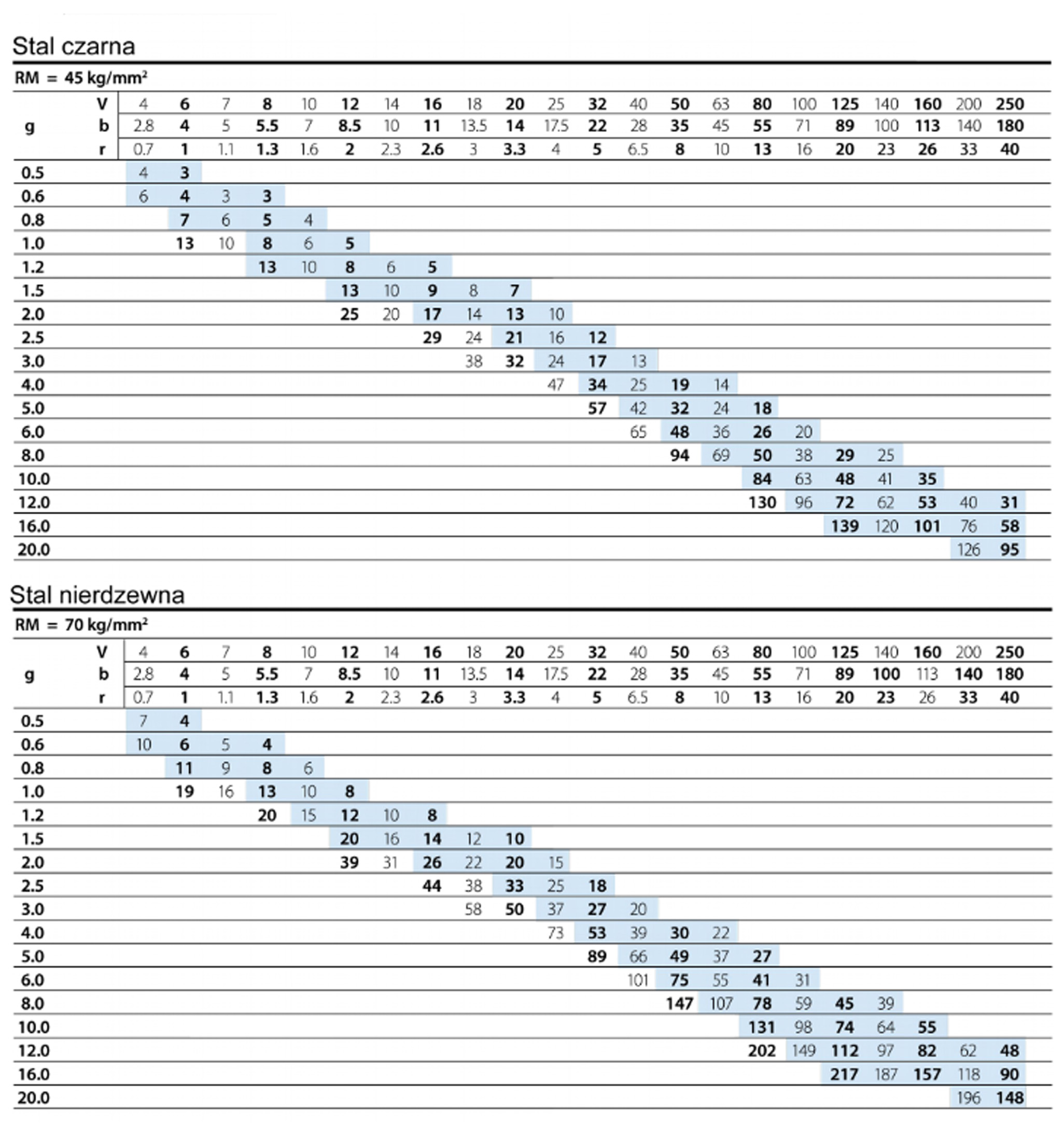