How does a sheet metal guillotine work?
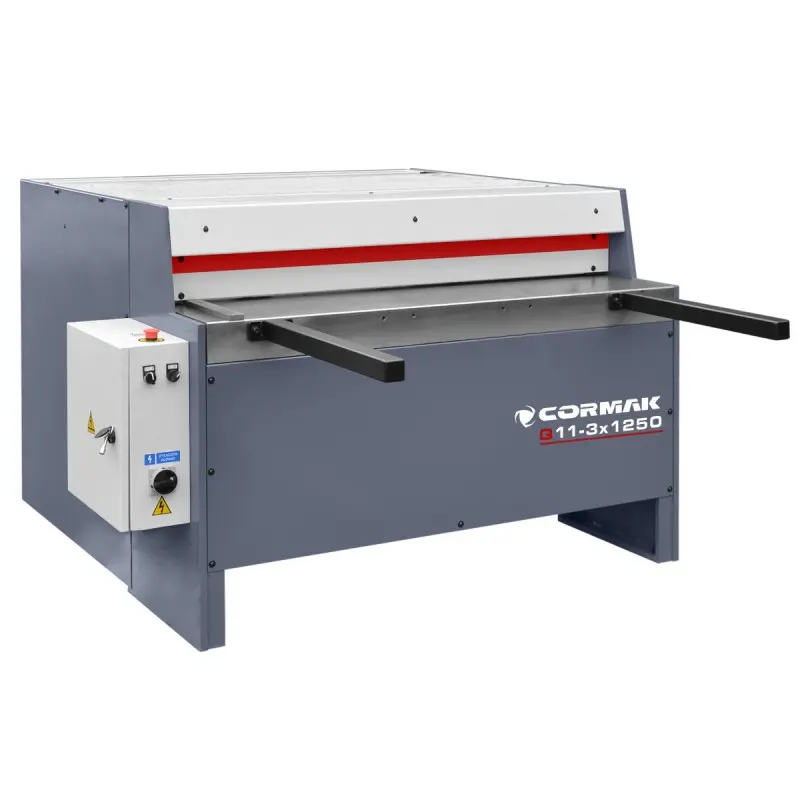
What is a Sheet Metal Guillotine?
A sheet metal guillotine is a precision industrial machine designed for cutting metal sheets of various thicknesses and sizes. Its name derives from its construction, resembling the French guillotine, but unlike its historical counterpart, this machine is used for the precise cutting of metals rather than wood or paper.
Sheet metal guillotine shears are equipped with two blades—one movable and one fixed—that enable fast, accurate, and straight cuts. The cutting process involves pressure exerted by the movable blade, which presses the sheet against the stationary lower edge. Thanks to a precise mechanism and significant force, guillotines can handle a wide range of materials, from thin aluminum sheets to thick steel plates.
Sheet metal guillotines are available in various models—from small, manually operated ones used in craft workshops to advanced hydraulic machines suited for industrial production.
How Does a Sheet Metal Guillotine Work?
The operation of a sheet metal guillotine is based on simple mechanical principles, yet it enables advanced industrial tasks. The cutting process begins with the placement of the sheet on the machine’s table, where it is securely held by clamps to prevent shifting during operation.
Once the material is positioned, the operator activates the cutting mechanism. In modern machines, such as those offered by CORMAK, the control system allows precise adjustment of parameters such as pressure force or cutting speed, ensuring accuracy and high-quality work.
The cutting process with a guillotine involves the following steps:
- The sheet is pressed against the stationary lower blade.
- The upper blade, driven mechanically or hydraulically, moves downward to cut the material with significant force.
- After the cutting motion, the blade returns to its original position, and the operator prepares the machine for the next cut.
Depending on the machine type, guillotine cutting can be fully automatic (CNC machines), where control is managed by software, or semi-automatic, requiring some operator input. Hydraulic guillotines can cut very thick materials, making them indispensable in the metal industry.
When to Use a Guillotine for Cutting?
Guillotine cutting is widely used across various industries, especially where precise and fast separation of metal sheets into smaller components is required. However, not every metalworking method is suitable for all conditions. Guillotine shears are particularly useful in the following scenarios:
- Mass production – Machines such as hydraulic guillotines or sheet metal shears enable quick cutting of large quantities of material, essential for serial production.
- Precision cuts – Adjustable cutting parameters allow operators to achieve perfectly straight sheet edges, critical for manufacturing structural components.
- Processing thick materials – Hydraulic guillotines can handle sheets several centimeters thick, making them essential in heavy industry.
- Metalworking shops – Smaller, manually operated guillotine models are suitable for craft workshops that require sheet cutting for individual projects.
Additionally, modern industrial machines from CORMAK, such as sheet metal guillotines, can process a wide variety of materials—from stainless steel and aluminum to copper and brass. This versatility makes guillotine cutting a reliable method for many industries.
Summary
A sheet metal guillotine is an indispensable tool for precise and fast cutting of metal sheets of various thicknesses and sizes. The cutting process is achieved by using a movable blade that exerts pressure to slice the material into defined pieces. Guillotine cutting is widely applied in both industrial manufacturing and metalworking shops. Its advantages include precision and versatility, enabling the processing of diverse materials. With modern technology and advanced control systems, operators can achieve perfect cuts with minimal effort.
As a manufacturer of industrial machines, CORMAK offers guillotines in various versions, allowing customization to specific production needs.