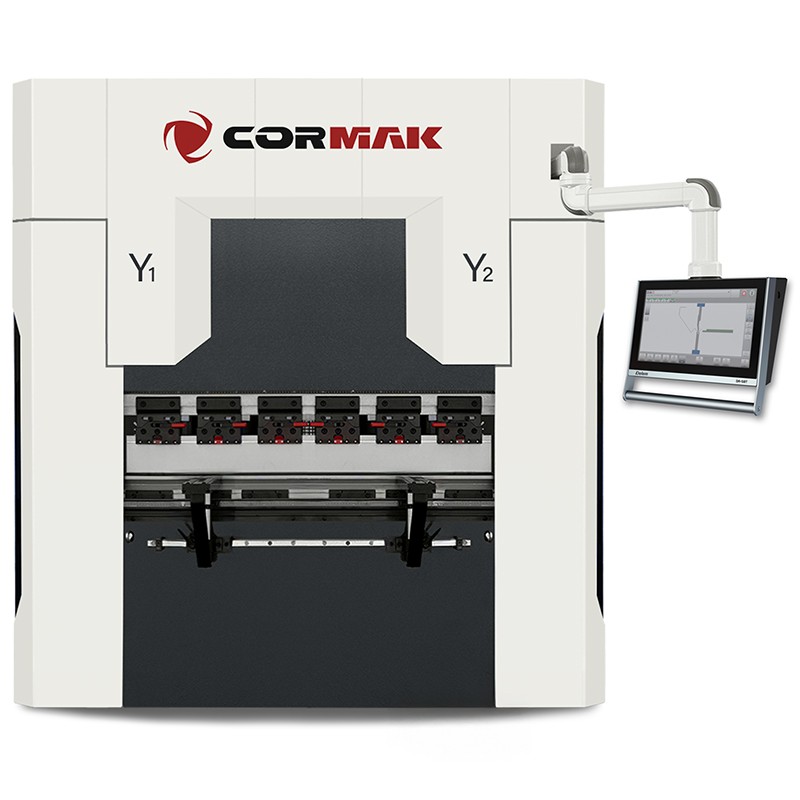
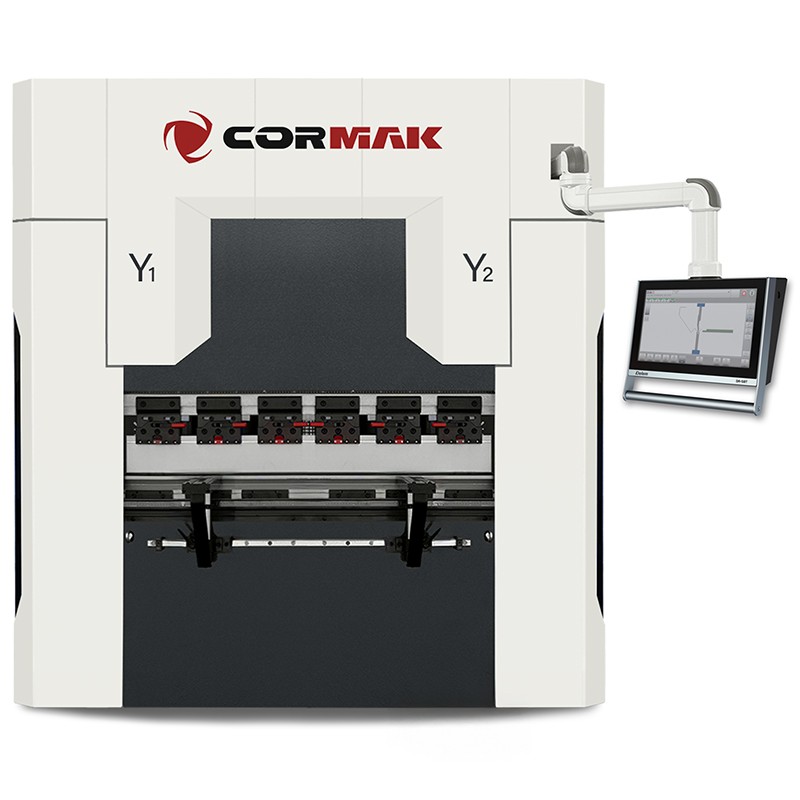
The basket is empty.
Servoelectric press brakes are modern devices used in sheet metal processing, which offer many advantages over traditional hydraulic presses.
Cormak press brakes are advanced devices enabling precise bending of sheet metal thanks to appropriately selected punches and dies. Our offer includes models equipped with DELEM DA-53TX controllers as standard and optionally DELEM DA53T, DA-58T, DA-66T, DA69T and CYBELEC 12 controllers, which provide a wide range of functions, enabling the implementation of the most demanding bending tasks.
Electric instead of hydraulic drive – Servo-electric presses use an electric drive, making them more energy efficient, quieter, and more precise than traditional hydraulic machines.
Increased precision – Thanks to servo technology, servo-electric presses provide higher edging accuracy, which is important in the production of parts requiring high precision.
Faster response and greater flexibility – The electric drive enables faster and more flexible adjustment of the pressing force and speed, which allows for optimizing the production process depending on the type of material and task.
Lower operating costs – Servo-electric presses are more energy efficient than hydraulic presses because they do not require constant hydraulic pressure or large oil tanks, which translates into lower operating costs.
Clean and No Oil Maintenance – Compared to hydraulic presses, servo-electric presses do not require hydraulic oil, which reduces maintenance costs and eliminates oil leakage issues.
Increased Reliability – With no complicated hydraulic system to break down, servo-electric presses are more reliable and require less frequent repairs.
Increased energy efficiency – Thanks to the use of servo motors, these presses consume energy only when operating, making them more energy efficient than traditional machines.
Easy integration with automation systems – Servo-electric press brakes can be easily integrated with automatic systems, which allows for full automation of the production process, including changing parameters in real time, which allows for faster adaptation to changing production conditions.
Operation silence – Thanks to servo technology, servo-electric presses operate much more quietly than hydraulic machines, which improves work comfort in production halls.
Better control over the bending process – Thanks to precise control over the movement of the press frame, the operator has full control over the bending process, which allows for repeatability and high quality of bends.
Servo-electric press brakes are becoming increasingly popular in the industry, mainly due to their advantages in terms of efficiency, energy saving and precision.
Max. thickness of bent sheet metal (S235) | up to 3.0 mm |
Nominal pressure | 600 kN |
Maximum length of bent sheet metal | 2000 mm |
Depth of cut-out in beams (throat) | 300 mm |
Maximum stroke of moving beam | 210 mm |
Maximum opening height | 410 mm |
Beam spacing | 1600 mm |
Rear bumper departure | 650 mm |
Engine power | 4 kW |
Length | 1800 mm |
Width | 1200 mm |
Height | 1850 mm |
Weight | 5000 kg |
Although the entire step bending process may seem quite complicated, the machines and software available at CORMAK are already at such an advanced stage that in many matters they completely replace the operator.
Ensures the same bending angle along the entire bending length - (option)
Ensures the same bending angle along the entire bending length - (option)
Manufacturer: Cormak
CORMAK JERZY ZALEWSKI
street Brzeska 120, 08-110 Siedlce, Poland
CORMAK CNC 40x1600 servo-electric press brake - DA-53TX
Servoelectric press brakes are modern devices used in sheet metal processing, which offer many advantages over traditional hydraulic presses. Cormak press brakes are advanced devices enabling precise bending of sheet metal thanks to appropriately selected punches and dies. Our offer includes ...More
CORMAK CNC 30x1250 servo-electric press brake - DA-53TX
Servoelectric press brakes are modern devices used in sheet metal processing, which offer many advantages over traditional hydraulic presses. Cormak press brakes are advanced devices enabling precise bending of sheet metal thanks to appropriately selected punches and dies. Our offer includes ...More
CORMAK CNC 70x2500 servo-electric press brake - DA-53TX
Servoelectric press brakes are modern devices used in sheet metal processing, which offer many advantages over traditional hydraulic presses. Cormak press brakes are advanced devices enabling precise bending of sheet metal thanks to appropriately selected punches and dies. Our offer includes ...More